Going Full Yellow
Extra! Extra! Read all about it! I’m kidding, just wanted to let you know that the blog is still alive. And now it’s time to present, at last, something new that I did in the last two years. I joined the team of Yellow Images in April 2015 to create exclusive 3D models for everyone who loves sports and needs simple but high-quality mock-ups to showcase awesome designs for teams and athletes.
I’ve been working on sports kits for these last 2-3 years, making highly detailed models ready for the final 10k rendition, like really, really detailed garments with geometric seam threads and complex textures. The cloth simulation actually started in 2012 with a shirt, when no one knew what’s MD and why we so badly need triangles. I still like what I do, the results, the process of updating my workflow, which is a bit slow, to be honest, wish it was like *poof* and it’s done. And yet, I’m getting better at it, referring to user feedback, which is always appreciated.
The process
So I kept learning and pushing the envelope, bit by bit, from a casual t-shirt to something like a fully-protected ice hockey player, which took me a month to simulate. Imagine the shoulder pads or a girdle under the player’s uniform, it’s not just shapeless bulges extruded from the skin, but a specially designed hard-shell protection (with padding) that requires special cut to make the jersey sit freely when moving. Layers of stretchable fabric to fit a complex mannequin. Should be easy, right?
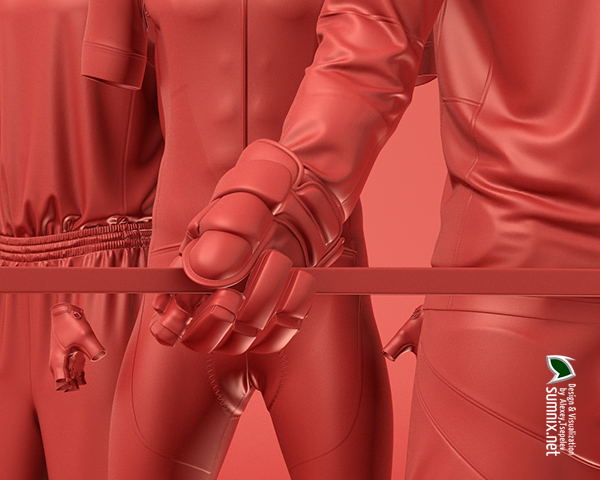
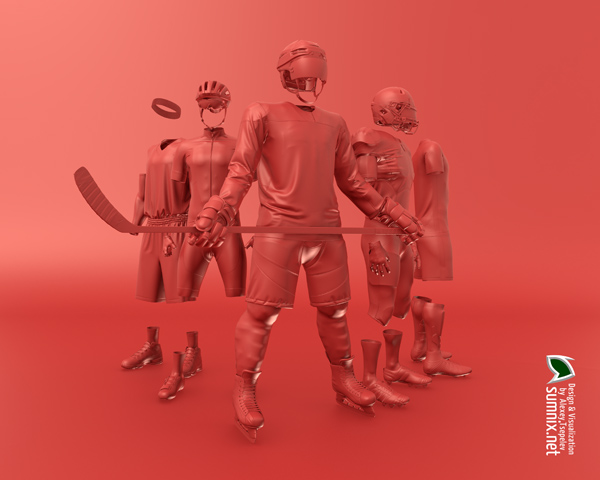
The meshes grew denser with more details. Recently I reached the maximum of 1 mm mesh, having installed more RAM, to create perfect folds in problem areas like armpits, this way it’s easy to get 5 million polygons per garment and 15 per full kit. Moreover, the textures became larger with every iteration, some models require insanely huge 16384 px textures. Different types of flat-locks and over-locks, buttons, zippers, name it, everything needs attention. Someone’d say that’s overkill, but I see the difference and it haunts me. That’s why a month, to make it almost perfect.
The content
Mostly it was all about the clothing, sports wear, casual, exotic, insanely difficult to render small parts in high-res (displacement!). In addition, there were accessories like an awesome umbrella cane (see below), sports equipment, headgear, footwear, and so on and on. Anything, that can contain design elements, should work a mock-up.
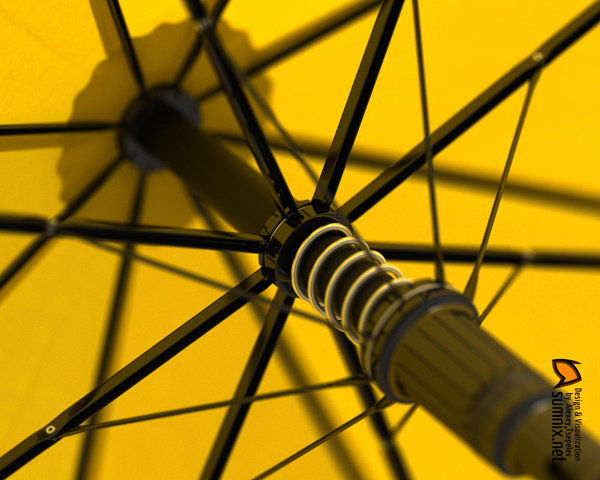
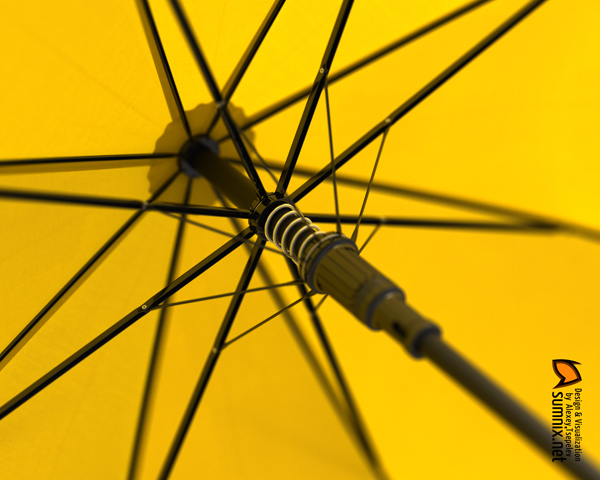
As an avid cyclist my favorite topic was about the jerseys and spandex-like fabric, which is, as always, way too whimsical to stay where it belongs without proper shapes of the panels. So yeah, the key to a good simulation is to get the right shape for, say, a shoulder panel or crotch area that bends over the thick seat pad sewn to it from the inside. Another interesting item to model was gloves, never the same. When modeling one (the other one will be mirrored) MD, again, reaches its limit of 1 mm mesh, which is bad news for the close-ups, the result is not as smooth as it should look and no retopology makes it better.
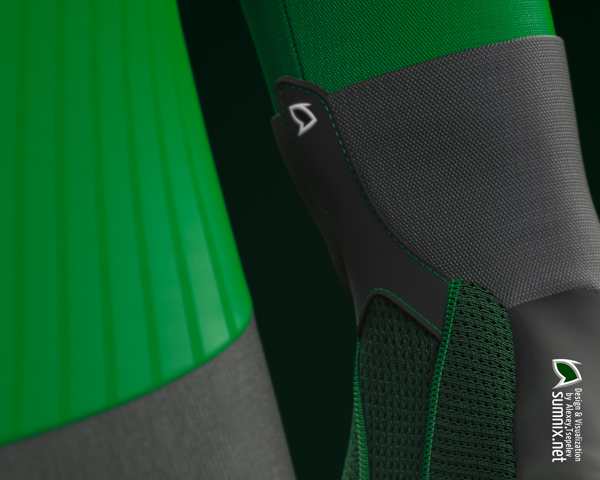
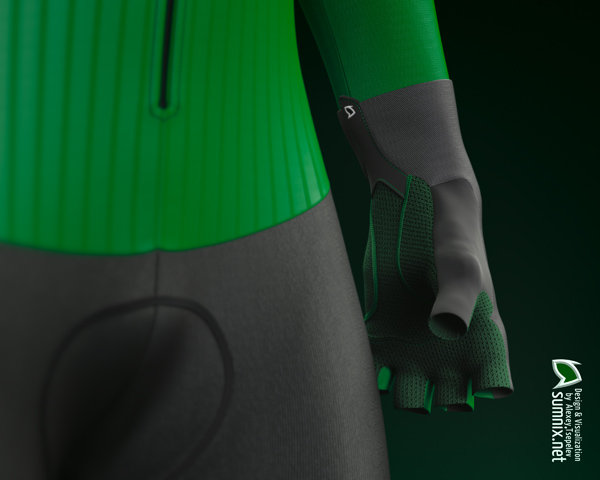
After all, it is just a matter of skills and time. One day you learn how to make routinely-boring steps faster, writing scripts and making the overall progress. And another day you see the flaws in your previous works (rly? you could do it better!), and you wish you would never know these things.
That’s it for now. New projects to come. I’m going to post a new video soon and restore my Behance account, which was deleted in 2012.
I say thankee-sai! Big-big!
UPDATE
Here’s a new video: